(翻譯:德化窯遺產(chǎn)文化研究院 孫延燕)
編者按:瓷器的工業(yè)化最早從中國開始,因此,對于早期的西方人來說,瓷器就是他們向往的詩和遠(yuǎn)方。
然而,當(dāng)時(shí)真正來過中國的西方人并不多。1935年5月,西方學(xué)者薩頓(Willard James Sutton)到德化瓷廠參觀,英國作家唐納利撰寫的《中國白—福建德化瓷》(《Blanc de Chine -Porcelain of Tehua in Fukien》)一書記錄了他當(dāng)時(shí)的見聞。
千年不斷的窯火成就了德化這樣一座特殊的城市,古老的匣砵及陶瓷碎片靜靜地述說時(shí)代的更迭。瓷都的時(shí)間似乎過得很快,發(fā)展日新月異;瓷都的時(shí)間似乎又過得很慢,古老的燒窯和陶瓷制作方式如今在此仍依稀可見,韻味雋永。
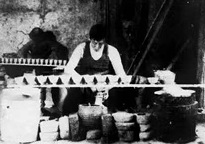
The softer rock which seemed to be a partially weathered feldspar was used for the body of the ware, the harder for the glaze. Seggars and fire bricks were made from the common surface clay of the neghbourhood, which is fairly refractory. The potters were using a low wheel, its upper surface not much more than a foot above ground, and set in motion by hand: it is interesting that a white porcelain ring was used as a bearing. The potters were little better paid than the farmers, sixpence a hundred for teacups was quoted by one man, who could earn perhaps four shillings a day by his labours. Moulds were used for figures in two halves, luted together before firing and with ornament, hands etc. added by hand. With the exception of spoons, which were packed in layers of rice hulls which being burnt smoulder for a long time, producing a soft biscuit ware, subsequently glazed and fired in seggars, the porcelain was a one-fire ware. After glazing the wares were dried on boards in rough sheds, packed in round seggars from 12 to 14 inches in diameter and stacked in the kilns, small lumps of clay and layers of ashes being used to prevent the glaze from sticking to the seggars.
較軟的巖石,似乎是部分風(fēng)化的長石,用于制造瓷器的胎體,而較硬的巖石則用于釉料。匣缽和耐火磚是用周圍普通表層粘土制成的,這種粘土相當(dāng)耐火。陶工采用慢輪制作,表面距離地面不超過一英尺,并用手使它轉(zhuǎn)動(dòng):有趣的是,白色瓷環(huán)有的被用作軸承。陶工的薪水比農(nóng)民略高,一個(gè)人一百個(gè)茶杯獲得6便士的價(jià)格,他可以通過自己的勞動(dòng)一天賺取大約四先令的收入。模具分成兩半用于制作人物雕塑,在燒制前粘合在一起,并添加裝飾、手等。除了勺子被包裹在稻殼層中長時(shí)間悶燒、燒成柔軟的瓷胎后在匣砵中一次性上釉燒制外,其它的瓷器都是一次性燒制的。上釉后,器皿放置在簡陋的棚子里的木板上晾干,然后放入直徑為12至14英寸的圓形匣砵中,小塊粘土和草木灰的使用可以防止釉料粘在匣砵上。